India’s engine development program has hit yet another roadblock because of the lack of a required testing facility and dependence on Russia which is currently caught up in the Ukraine war.
The Kaveri Dry engine is a non-reheating non-afterburner derivative of the indigenous Kaveri military gas turbine aero engine that has been under development since 1989 at the Gas Turbine Research Establishment (GTRE) of the Defence Research and Development Organisation (DRDO), Frontline Magazine (The Hindu) reported.
The 52-kilonewton dry variant engine is supposed to power India’s first stealth, unmanned combat aerial vehicle (UCAV), the Ghatak which is said to weigh less than 15 tonnes and capable of flying at altitudes of 30,000 ft (9,144 m).
India wants to conduct simulated high altitude tests which would simulate high altitude conditions on the ground.

Once the engine clears these tests, it will then be subjected to flight testbed (FTB) testing which would involve the GTRE placing the engine in a modified Ilyushin (Il)-76 fixed-wing, four-engine turbofan aircraft based in Russia’s Gromov Flight Research Institute near Moscow.
Plagued Engine Development
Frontline reported that GTRE had hoped to complete all tests by 2024-25 and begin limited series production by 2025-26, however with Russia fighting the war in Ukraine, the tests will take longer to materialize which had already been delayed because of the COVID-19 pandemic.
Since the 1990s, the Kaveri dry engine has been taken to Russia several times for testing.
In 1986, the GTRE in Bangalore launched its Kaveri afterburning turbofan engine project, to power the indigenous Light Combat Aircraft (LCA), approved three years earlier.

However, during the high altitude trials in Russia in mid-2004, the Kaveri was found inefficient and overweight and the LCA program then switched to the US General Electric GE-F404IN engine which powers the LCA FOC version and the Mk-1A.
Despite these setbacks, GTRE was provided the additional funding of about Rs 28.39 billion in late 2004 from the Ministry of Defense (MoD) for the Kaveri Programme, this time with the renewed aim of designing a fighter engine with a thrust of 93-100 kiloNewton (kN) to offer the projected platform greater maneuverability, angle of attack and improved payload capability.
However, in 2010, the MoD listed five reasons for delays in Kaveri’s development which included, technological complexity, lack of critical equipment and materials, engine technology denial by advanced countries, absence of domestic testing facilities, and, above all non-availability of skilled and specialized manpower.

So, the more advanced versions of the LCA that are to be manufactured domestically and would require a more thrust capacity, will be powered by the more powerful GE-F414 engines.
Whereas for the Kaveri engine, it was decided that its derivatives will be developed to power tanks, railway locomotives, naval ships, and the DRDO’s under-development ‘Ghatak’ UCAVs (Unmanned combat aerial vehicle), however not much has come out of it.
Lack Of Expertise & Indigenous Testing Facilities
The problem is, that developing a high thrust low bypass turbofan for military applications requires deep expertise across combustion, fluid dynamics, materials, and control theory applied, tested, and repeated continuously over years.
The knowledge of the underlying technologies is not available in any textbooks but is a closely guarded property of a handful of corporations.
Furthermore, while India aspires to become the part of the club of a few global aviation majors who have mastered gas turbine aero-engine technology, it does not even possess a fully functional wind tunnel facility that is essential to study the aerodynamic characteristics of its designs.
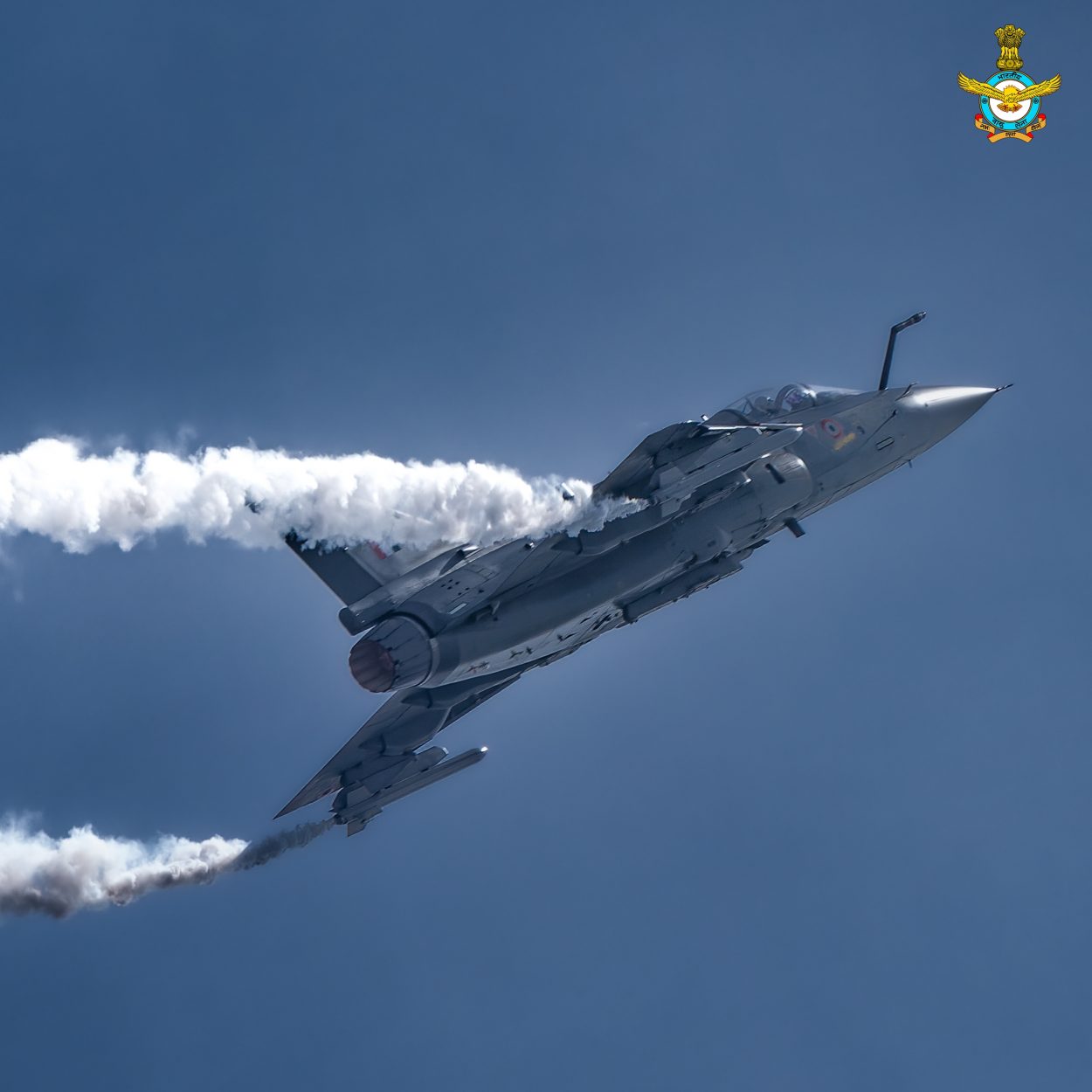
Once designed and assembled, engines need extensive testing in wind tunnels and subsequently on flying testbeds for hundreds and thousands of hours to understand the fatigue characteristics as well as degradation of each part.
Such a facility can simulate and test an engine designed to work at 40,000 to 50,000 feet above the ground and will give designers the freedom to scale up or down, and test and validate the hundreds of components.
Frontline reports, that the DRDO scientists have confessed that the lack of such a facility means that an engine being indigenously designed has to be carted to Russia or elsewhere, making it a time-consuming process.
Also, for several years now, scientists and designers have been pushing for the acquisition of an Il-76 aircraft to be used purely as an aero engine flight testbed, but to no avail, and after more than 30 years of the Kaveri Engine project was launched, the engine continues to remain under development.
- Written by Tanmay Kadam/EurAsian Times Desk
- Contact the author at etdesk@eurasiantimes.com
- Follow EurAsian Times on Google News