Air Marshal Anil Chopra (Retired)
Just last week, the US Defence Advanced Research Projects Agency (DARPA) okayed the construction of an X-65 plane with air-jet flight controls, a new technology that replaces moving control surfaces with Active Flow Control (AFC) actuators that use jets of air for control.
The contract has been awarded to Aurora Flight Sciences, a Boeing company, to build a full-scale aircraft called the X-65. DARPA hopes to one day replace all those expensive, heavy control surfaces with a much simpler system that depends on jets of air.
If successful, it could be a game-changing leap.
Evolution of Aircraft Flight Control System
If you have ever sat on the window seat of a plane, you would have probably noticed a lot of activity on the wings, a complex symphony played by control surfaces.
Interestingly, they are controlled by an intricate system hidden in the aircraft. Flight controls are required to control an aircraft’s direction and speed in flight. Aircraft engine controls are also considered flight controls as they change speed.
A conventional fixed-wing aircraft flight control system (AFCS) consists of flight control surfaces, cockpit controls, connecting linkages, and the necessary operating mechanisms and computers.
The very first controlled, sustained flight of an engine-powered, heavier-than-air aircraft by the Wright Brothers in 1903 had some systems of aircraft control. The current layout of the flight control system evolved by April 1908 and was used on Louis Blériot’s Blériot VIII monoplane.
The primary cockpit flight controls have a control (yoke) in the center or on the side of the pilot. It controls the role by deflecting ailerons and pitch by moving the elevator. The Rudder pedals control yaw by moving the rudder.
The thrust lever or throttle controls engine speed or thrust for powered aircraft. The cockpit controls were initially connected to the surface mechanically using rods and cables.
As speeds and aerodynamic loads increased, hydro-boosters and later electric signaling (fly-by-wire) through a computer were introduced. At this stage, artificial feel devices were introduced so that the pilot would not inadvertently over-stress the aircraft because very little force or displacement would significantly move the control surface.
The electric cables were later replaced by fiber-optic cables. Also, redundancies were introduced by having more than one hydraulic or signaling system. In some cases, the control surfaces could be combined, as in a V-tail ruddervator or elevens and flaperons, and these hybridized the movements and effects.
There are also some secondary controls like flaps, air brakes, leading edge slats, spoilers, and trim tabs. Some planes also have variable-sweep wings. These change wing profiles to vary lift and drag for specific flight regimes and help the pilot exercise finer control or ease the workload.
Recent Research Approach to Control Systems
Several technologies are being researched to integrate the functions of flight control into the wings itself. Elastic materials could allow flexible wings to change aerodynamic shape in flight.
These are also known as the “adaptive compliant wings” or “morphing aerofoils.” The X-53 Active Aero-elastic Wing was a US Air Force, NASA, and Boeing effort. Notable efforts have also been made by FlexSys, who have conducted flight tests using flexible aerofoils retrofitted to a Gulf Stream III aircraft.
This would remove control surfaces and the hinges and improve aerodynamic efficiency. These could mimic the natural flexing of birds’ wings in flight. Passive Aeroelastic Tailoring (PAT) is being considered for high aspect ratio wings.
The second approach has been related to fluidics. A few decades back, some aircraft incorporated systems such as blown flaps. Part of the air from the aircraft compressor was diverted to blow over the flaps to increase efficiency. Air was also blown over the wing to delay boundary layer separation and thus increase lift.
But the new approach is that larger and more complex mechanical parts be altogether replaced by smaller, simpler, fluid slots that emit air flows through many small jets to change the direction of vehicles.
This active flow control promises simplicity, reduced mass, costs much less, and reduces inertia and response times. A variant of this was demonstrated in the Demon UAV, which flew for the first time in the UK in September 2010.
The DARPA AFC Project
DARPA and a Boeing subsidiary, Aurora Flight Sciences, have begun building the first full-scale X-65 aircraft using active flow control (AFC) actuators to demonstrate a new method of flight control that uses no external moving parts.
The uncrewed aircraft with diamond-shaped wings is an experimental jet being developed under the Control of Revolutionary Aircraft with Novel Effectors (CRANE) program overseen by DARPA, the Pentagon’s research and development agency. The Micro Adaptive Flow Control program of DARPA helped pioneer the foundational understanding of fluid dynamics that eventually led to CRANE. AFC technology will alter the aircraft’s aerodynamic flow field to add energy or momentum to the flow of air over the aircraft.
The CRANE program aims to do away with all control surfaces and develop an aircraft controlled fully by jets of pressurized air that alters the surrounding air flows over the aircraft while in flight. It will reduce mechanical complexities and create more real estate on board for other important/combat systems.
Non-moving external surfaces will also greatly improve stealth capability. The AFC could revolutionize both military and commercial craft in the future.
DARPA AFC Project Nozzle Layout
At an experimental stage, to reduce risk, the first X-65 demonstrator will feature both conventional moving control surfaces and the AFC actuators using the jets of pressurized air.
A set of 14 AFC banks with independently controllable air supply channels will be included in the craft. Sensors across the airframe will monitor how the AFC effector’s performance compares with traditional control mechanisms. As the tests proceed, the mechanical controls will be locked down and replaced selectively until the AFC system has full control.
The X-65 will have a 30-foot (9-meter) wingspan and weigh 7,000 pounds (3,200 kg), roughly the size of the U.S. T-38 trainer aircraft. It flies till Mach 0.7. The distinct diamond-shaped design will increase aircraft strength.
Preliminary tests, including critical design review, wind tunnel testing, and scale-model construction, have already been completed. The X-65 is already under fabrication; roll-out is planned for early 2025, and the first flight will be by mid-2025.
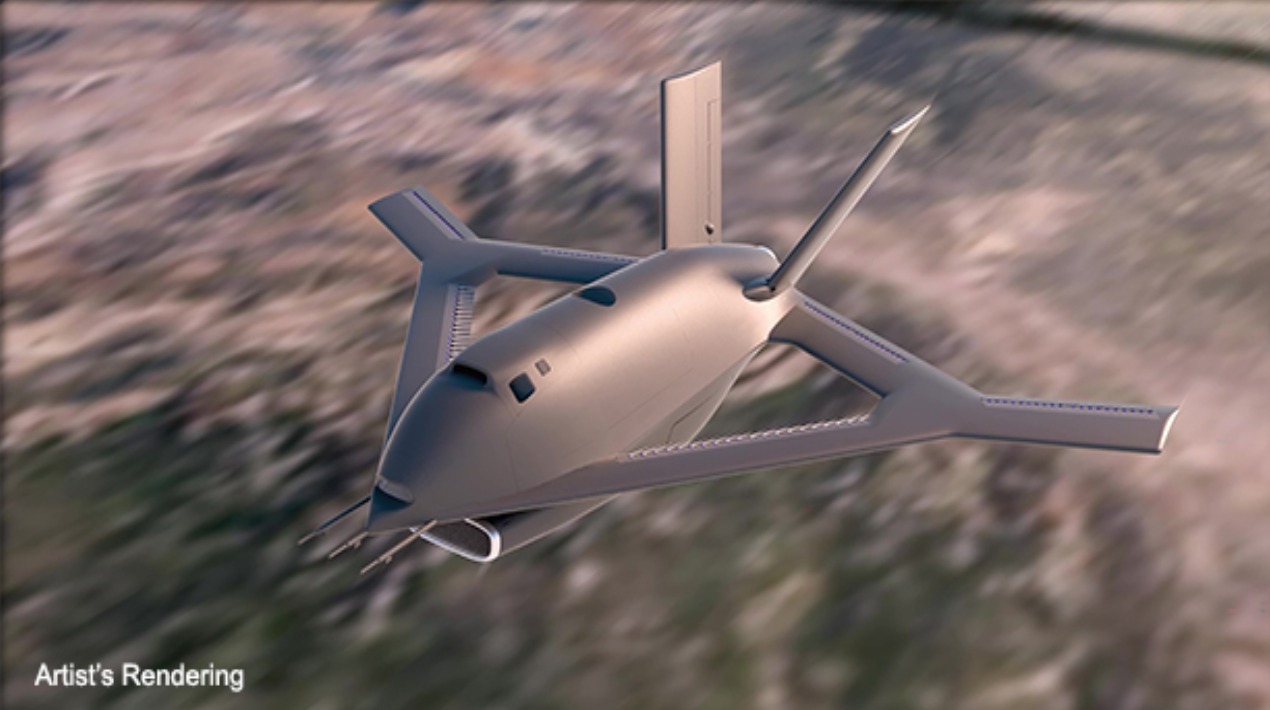
The AFC system uses an array of nozzles installed at the ends of aerofoils. The effectors will be embedded across all the lifting surfaces. By shooting compressed air out of these nozzles, they can change the air pressure in the vicinity and alter the airflow over the aerofoil.
In this way, the system can change the roll, pitch, and yaw of the aircraft. The AFC actuators could one day replace all expensive and relatively heavier control surfaces with a much simpler system that uses jets of air to do the same thing.
Once certified, the technology will allow making airframes lighter and sturdier. New aircraft could have thinner, longer wings with much greater efficiency. The technology could also be applied to the fuselage to generate more lift and reduce drag.
BAE Systems AFC Research
BAE Systems has successfully tested flap-free flight technology intended to enhance military capability as part of a DARPA-funded project.
A 3D printed titanium model was put through its paces to physically test its aerodynamic characteristics in a high-speed wind tunnel. The test helped understand the potential cost, weight, and performance benefits that flow control technologies could provide.
The digitally designed, full-scale AFC model and prediction software will support pushing the design to the limit. The wind tunnel testing has validated terabytes of data, helping to mature significant aerodynamics research in computer fluid dynamics.
Game-Changing Way Ahead
The X-65 breaks the century-old design paradigm for flight controls. A new method of flight control that uses no external moving parts will be a great leap in aircraft design. It will greatly reduce weight and save volume.
It will significantly contribute to stealth. The stage is still experimental. Advanced manufacturing robotics and digital engineering would hasten the program. The X-65 concept will revolutionize both military and civil aircraft of the future. Physically it may first be employed on fighter planes. It could come on board airliners in 6-8 years.
In India, the National Aeronautical Laboratory (NAL) and the Indian Institute of Science (IISc), both based in Bengaluru, are carrying out research on fluid dynamics. Most IITs are looking at the subject.
Prof. Satish Dhawan, former Chairman of ISRO, is regarded as the father of experimental fluid dynamics in India. He was one of the most eminent researchers in the field of turbulence and boundary layers, and is credited for setting up the first supersonic wind tunnel in India at IISc.
BITS Pilani unveiled India’s most significant and largest (5 m) cutting-edge wind tunnel facility in September 2023. The NAL has a 1.2 m trisonic and 1.5 m subsonic wind tunnels.
India has still to reach the level of funding that the US DoD and NASA can afford. However, the government’s Atmanirbharta (self-reliance) push will get us there faster.
- Air Marshal Anil Chopra (Retired) is an Indian Air Force veteran fighter test pilot and is currently the Director-General of the Center for Air Power Studies in New Delhi. He has been decorated with gallantry and distinguished service medals while serving in the IAF for 40 years. He tweets @Chopsyturvey
- Follow EurAsian Times on Google News